Silica sand washing plant process flow and equipment cost
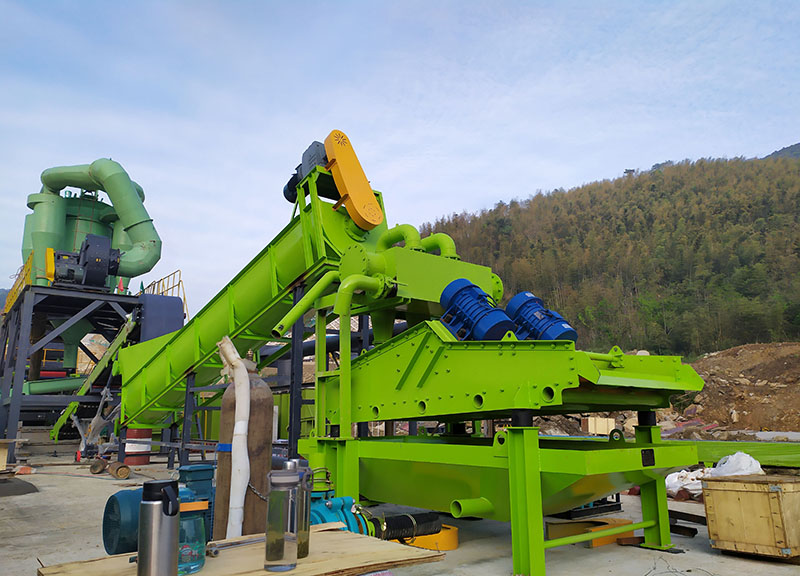
Silica sand washing plant for silica purification
Quartz sand, also known as silica sand, can be made into high-purity quartz sand after beneficiation and purification, which is used in glass, ceramics, metallurgy, casting, frac sand washing and refractory industries.
After silica sand washed by a beneficiation plant, it can meet the industry standards. Artificial sand and natural sand contain certain impurities. It is necessary to use the quartz sand washing plant to clean the impurities in the prepared sand to complete various construction requirements. The quartz sand washing equipment has been exported to Saudi Arabia, Thailand, Malaysia, South Africa, Australia, Europe, etc.
Working principle
Purification process of silica sand
The process of cleaning silica sand is crushing, washing/, magnetic separation, acid leaching, washing, dehydration, and drying.
water washing
Washing sand recycling machine working principle. After the natural silica sand is classified and filtered by the screening equipment, the qualified products flow into the spiral sand washing machine through the launder or the pipeline. It is fully cleaned, soaked and broken by a screw mixer (for larger muddy and extra-large effect), sandstone is fully separated from impurities and mud.
Fine sand and muddy water are deposited in the tail of the spiral washing, and the recovery of fine sand is achieved through a concentration and recovery device. Then the coarse and fine sand enters the wheel washing machine at the same time for secondary cleaning to achieve complete separation of the sediment.
Scrub
With the help of mechanical force and the grinding and peeling force between the sand grains, the thin film iron, adhesive and muddy impurity minerals on the surface of the silica sand are removed, and the unconstituted mineral aggregates are further smashed, and then the classification operation is performed to further purification.
Pickling
If the finished sand has a high iron content, it will enter the pickling process. First, it will be washed to remove powder and impurities, and then pickled, soaked and washed, dried or cooled.
Magnetic separation is mainly used to remove magnetic minerals in silica sand. For example, weak magnetic minerals such as hematite, limonite, and biotite can be removed by a strong magnetic machine, while strong magnetic minerals such as magnetite can be subjected to weak magnetic separation. Machine removed. Flotation is used to remove some impurities that cannot be removed by magnetic separation, such as feldspar and mica in silica sand, to further improve its purity.
Then the coarse sand is lifted into the high-frequency dewatering sieve feed end by the impeller of the wheel washing machine, and the overflow mud water flows into the high-frequency dewatering sieve water tank through the pipeline and then is recycled into the high-frequency dewatering sieve through the concentration and separation device. The vibration of the sieve is dehydrated, and finally, the sandstone is cleaned, recovered, dehydrated and discharged.
Product Features
The green and environment protection sand washing production line is a system solution for the problems of sand dewatering, tailwater purification, waste dry discharge. The silica sand washing plant mainly includes screening, cleaning, dehydration, fine material recovery, solid-liquid separation, sludge dewatering, and other aspects. The material is effectively screened, washed and dewatered throughout the system. Save resources and reduce water consumption. The entire production line has excellent continuous working performance and convenient maintenance. Long service life, easy to move and excellent effect. At the same time, it ensures no pollution and meets environmental protection requirements.
Equipment for silica sand washing
Crusher: jaw crusher, cone crusher, sand-making machine.
Sieve: It can be used with a circular sieve or a roller sieve.
Sand washing machine: Through the sand washing and recycling machine, the washing, dehydration and recovery of the material under the sieve after the sieve is obtained by the circular vibrating screen.
In order to meet environmental requirements, it is possible to install a concentration tank and a filter press to achieve tail water purification.
Concentration tank: Separation of mud and water by concentration and sedimentation to achieve tail water purification.
Filter press: The sludge from the concentrated tank is pressed into a mud cake by a filter press to achieve sludge dewatering and a dry heap.
The silica sand washing plant cost
A 100 ton per hour silica sand purification plant in cost about 150,000 USD.
Product Advantages
(1) Extracting the fine material in the raw material slurry firstly can effectively reduce the load of the subsequent equipment and reduce the type of the equipment, thereby achieving the purpose of small investment and small floor space, reducing wear and tear on the equipment and prolonging the service life.
(2) The fine sand recovery machine has reasonable waterway design, including backwater regulation and overflow regulation, which makes the recovery effect of the whole machine more ideal. The internal structure of the concentration tank is designed according to the principle of fluid dynamics, fully considering turbulence and settlement. In other aspects, in the case of the same amount of processing, the volume is smaller, and the amount of flocculating agent is more economical; the filter press adopts fully automatic program-controlled pulling plate technology, and a pressure gauge and an overpressure protection reflux device are installed at the feeding port, which is effective. The protection device components and the filter cloth do not work under overload conditions.
(3) Patent design, reasonable process, optimized structure, water and mud after treatment can meet national environmental protection requirements.
Technical parameters
Model | Feed size (mm) | Imp diameter (mm) | Screen size (mm) | Spiral diameter (mm) | The amount of sand released (t/h) | Secondary separation | machine power (kw) | weight (kg) | Dimensions (mm) with pump and motor |
DS-LX09-26-1530J | ≤10 | 2600 | 1500*3000 | 920 | 40-120 | yes | 66.5 | 11560 | 14550*5710*4150 |
DS-2LX09-30-2442J | ≤10 | 3000 | 2400*4200 | 920*2 | 80-180 | yes | 129 | 21450 | 16220*6670*4500 |
DS-2LX09-30-2448J | ≤10 | 3000 | 2400*4800 | 920*2 | 80-180 | yes | 129 | 21860 | 16850*6670*4500 |
DS-LX11-30-1836J | ≤10 | 3000 | 1800*3600 | 1120 | 80-150 | yes | 104.5 | 18030 | 14580*5542*4500 |
DS-LX11-30-1842J | ≤10 | 3000 | 1800*4200 | 1120 | 80-150 | yes | 104.5 | 18450 | 15200*5860*4500 |
DS-2LX11-36-3048J | ≤10 | 3600 | 3000*4800 | 1120*2 | 150-250 | yes | 172 | 35800 | 17681*8090*4500 |