Users who have used linear screens should have a better understanding of the large processing capacity, long service life, light weight and simple structure of linear vibrating screen. Linear vibrating screens have been widely used in sand production and ores preparation plants. But there are various problems affecting the service life of screens in operation. Then, summarized how to effectively extend the service life of linear screens as follows.
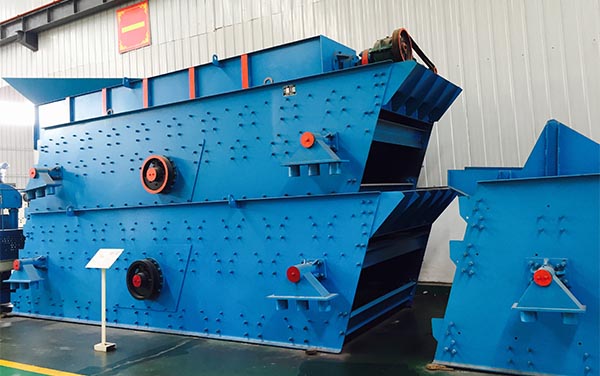
Factors that affecting service life
Generally, in the daily operation of horizontal linear screen, the damages of screen machine parts is basically divided into two types, one is crack and the other is fracture; the concrete part is in the middle part of screen beam, the side plate of machine and the part of fixed willow Nail; in the actual production and processing, the production process, beam structure design, beam material and other factors lead to cracks or even fractures of beam, which will affect the stable operation and service life.
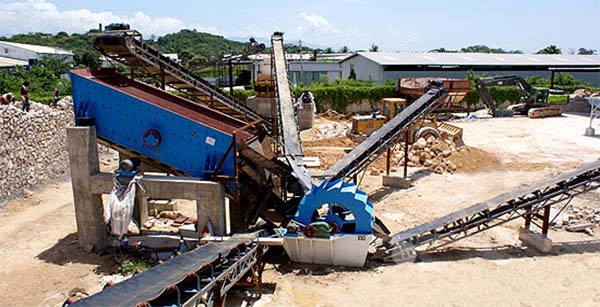
How to extend the service life of linear vibrating screen?
1. Checking whether the linear screen mesh is tight, the seal is damaged, the vibration motor lubricating oil is good, the bolts of each component are loose, the transmission device is stuck, etc.; When the sieve machine is working, it should be kept idling first. After the sieve machine runs smoothly, it can be fed. When feeding, it should be evenly distributed to reduce the screen net to meet the extended screen life; The material in the sieve frame is completely screened, and the residual materials inside the sieve frame are cleaned in time for the next use.
2. Linear screen must be started without load, and the material can be started after the sieve is running smoothly. Before shutdown, the feed should be stopped first and material on sieve surface should be drained. This is because the residual material inside screen will corrode sieve frame and screen mesh to affect the service life; The output of screening is large, so the loss of screen and the loss of bouncing ball are also relatively large, and it is also necessary to check frequently. The production of some enterprises is assembly line operation, and the screening will works 24 hours a day. This requires the operator to make a handover record when handing over the shift, recording the output of sieve machine during use, the problems encountered during use and solutions.
3. Checking the tightening degree of all bolts, and re-tighten once after the initial work for 7h; the feed chute should be as close as possible to feed end, and as far as possible, feed the material along the full width of sieve as much as possible. The running direction of material on sieve surface is the same, so as to obtain the best screening effect; the maximum drop of feed point to screen surface is not more than 450mm, ensuring the minimum impact of material on screen surface.