Banana screen is a new type of screening equipment. The screen has large processing capacity and can be used for wet and dry screening to replace conventional inclined screens or horizontal screens. So far, two types of banana screens with single-layer and double-layer screens have been developed, and have been popularized in beneficiation and coal preparation plants. Compared with the conventional screening machine, the main advantage of the banana screen is that when the same area of the screen surface is used, the processing capacity of the material can be greatly improved. The screen has been widely used in mineral processing and coal preparation plants that require increased screening capacity but cannot use large-volume screening machines due to plant space constraints.
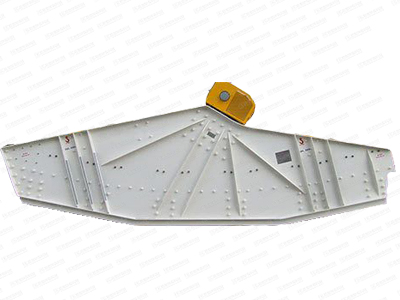
The working principle of the banana sieve is similar to that of the single-layer thin sieve in some respects. The inlet end is an inclined surface, and the rear part is composed of several different inclined sections, and the inclination angle is 100° at the discharge end. The inclined surface of the banana screen is steep at the inlet end, and the material can pass through at high speed, which is beneficial to reduce the thickness of the bed. When the material of larger particle size is passed quickly, the layering time is short, and the material smaller than the sieve size is the most likely to be close to the screen surface and quickly pass through the sieve; The running speed of large-size materials slows down. At this time, materials with a slightly smaller dry sieve size will also randomly pass through the sieve. It can be seen that it is most suitable for screening and grading materials with a large content of fine particles. According to experience, the processing capacity of fine-grained materials with a particle size of less than one-half of the sieve opening size can be doubled compared to conventional sieves.
The screen surface of the banana screen uses metal wire mesh or polyurethane material. The main difference between it and the conventional screen is the setting of the screen surface. In order to increase the penetration rate of the inclined surface of the feed end, the banana screen has a long groove with movable sieve holes, and its length-to-width ratio is 4:1, which has a good penetration rate for fine particle screening. As the inclination angle of the banana sieve gradually decreases, the length of the slot is continuously reduced, reaching the minimum at the discharge end, thus forming a square or hexagonal sieve hole, this sieve hole pair is slightly smaller than the sieve hole size The granular material has a higher penetration rate.
The development of banana sieve
At present, Australia is the world leader in the research and development of banana sieve. Its main characteristics are as follows. The Australian banana sieve has a novel design, and the design of the sieve surface presents multi-sloping section changes to reduce the angle change between the sieve plates. The banana screen originally designed has 3 inclined sections and the angle change is 12.
Field use has proved that the sieve concentrates wear points in the section where the angle changes, and the newly designed banana sieve can significantly reduce the wear section by subdividing the angle in a wide range.
Using polyurethane material, this standard new material screen has the advantages of anti-wear and easy replacement, and because the screen surface of this material is a flat plate, it is helpful to install a vibrating feeder at the front of the screen, so that the feeder can adapt to The screen width effectively ensures that the feed is evenly distributed along the full screen width.