Small membrane filter press, low middle capacity filter machine
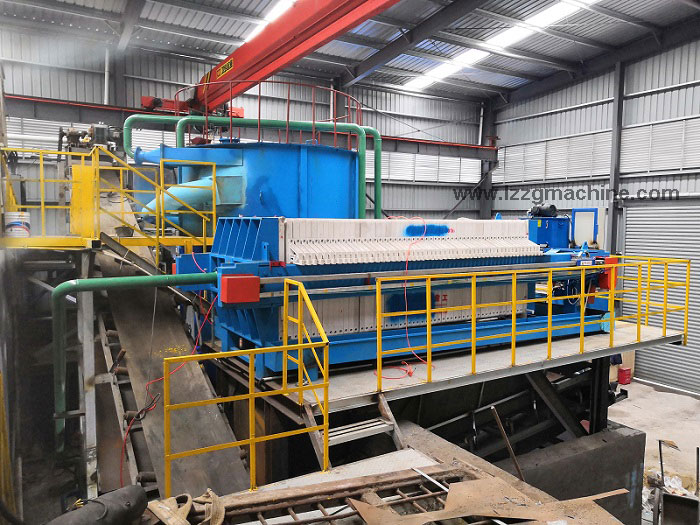
The main difference between the membrane filter press and the ordinary box filter press is that two elastic membranes are added on both sides of the filter plate (the composite rubber diaphragm is the integral diaphragm). During the operation, when the feeding is finished, The high-pressure fluid medium is injected into the membrane plate, and the entire membrane is bulged to press the filter cake to achieve further dewatering of the filter cake, which is press filtration.
Working principle
The membrane filter press, that is, the diaphragm filter press, is a filter press with an elastic membrane between the filter plate and the filter cloth. During use, when the feed is completed, a high-pressure fluid or a gas medium can be injected into the membrane plate, and the entire membrane will bulge the filter cake, thereby further dewatering the filter cake, which is commonly referred to as press filtration.
The first is positive pressure and strong pressure dewatering, also known as slurry dewatering, that is, a certain number of filter plates are closely arranged in a row under the action of strong mechanical force, and a filter chamber is formed between the filter plate surface and the filter plate surface, and the filter material is strong. The filter material that is sent to the filter chamber under positive pressure and the filter material entering the filter chamber is trapped by a filter medium (such as filter cloth) to form a filter cake.
Product Features
The membrane filter press has the advantages of high pressing pressure, good corrosion resistance, easy maintenance, safety and reliability, etc. It is metallurgy, gas,
The first choice for customers in the paper, coking, pharmaceutical, food, brewing, fine chemicals and other industries.
Filter presses have been widely used in various fields where solid-liquid separation is required. Diaphragm filter presses are considered an alternative upgrade to conventional van filter presses.
The Membrane filter press has a good effect in terms of processing capacity per unit area, reducing the moisture of the filter cake, and adapting to the properties of the treated material.
The Membrane filter press is applied to sludge and sewage treatment. The minimum moisture content of the filter cake has been less than 60%. Compared with the traditional box filter press, the filter cake has a solid rate higher than 2 times, and the filter cake transportation cost greatly reduced.
Technical parameters
Model | Feed concentration (%) | Filter area(m²) | Power (kw) | Capacity(t/h) | Weight (kg) | Dimension (mm) |
G50-80 | 20-40 | 50 | 15 | 1-1.5 | 3456 | 4110*1400*1230 |
G80-80 | 20-40 | 80 | 15 | 1-2 | 4584 | 4990*1400*1230 |
G100-100 | 20-40 | 100 | 24 | 2-3 | 6628 | 4900*1990*1600 |
G150-125 | 20-40 | 150 | 27.5 | 3-5 | 9800 | 6010*2000*1600 |
G200-125 | 20-40 | 200 | 35.5 | 4-6 | 12500 | 7050*2260*1600 |
G250-125 | 20-40 | 250 | 44.5 | 5-7 | 14000 | 7890*2260*1600 |
G300-125 | 20-40 | 300 | 52.5 | 6-8 | 25000 | 8800*2260*1925 |
G400-150 | 20-40 | 400 | 62.5 | 9-11 | 30000 | 10670*2260*1925 |
G500-150 | 20-40 | 500 | 82.5 | 11-12 | 36500 | 12350*2260*1925 |